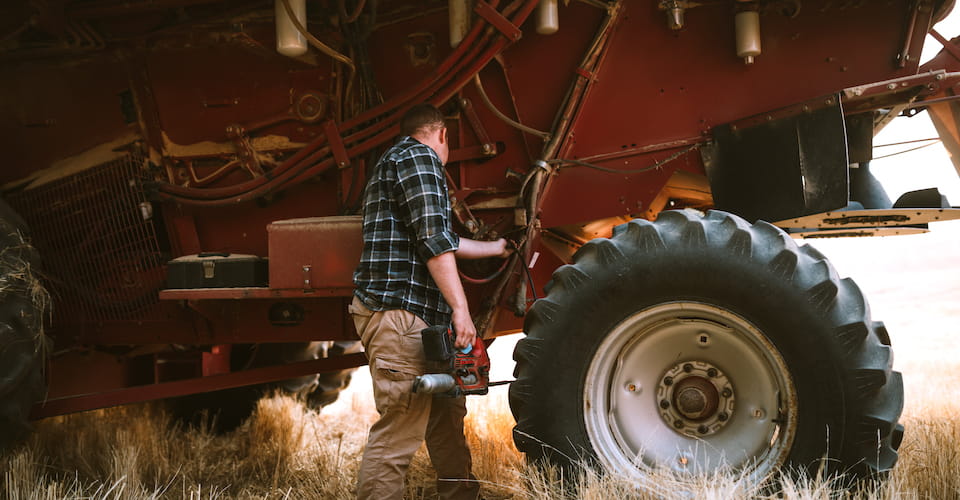
When it comes to the products your operation relies on, grease is a non-negotiable that keeps your equipment running smoothly. Using the right grease can extend the life of your equipment and enhance your operational efficiency. And with the grease market continuing to see pressure on labor and raw materials, causing delays and affecting availability, it’s more important than ever to find the right supplier with a robust portfolio of products that can fully support your operation.
So how do you know which grease is right for your operation? There are many factors to consider when selecting grease, and it’s often a more complex product than one might think. You’ll want to ask yourself questions like: How will it be used? Are the greases you’re choosing compatible with each other? What makes a grease high quality?
Let’s answer these questions and arm you with the knowledge to make the right choice to protect your investments.
1. Understand your environment
Not all lubricants are created equal, especially when it comes to grease. Greases have different properties based on their chemistry, so it’s important to keep in mind the role of grease and how it’s used on your operation. Ask yourself these two questions:
a. What conditions will your grease need to withstand?
This can range from exposure to water and dirt to extreme hot and cold temperatures. If you’re not using the proper grease to withstand these conditions, you’re likely to encounter serious issues like overheating and excessive wear, both of which can lead to equipment failure.
b. How will your grease be used?
Consider areas of application, like gears and bearings, as well as the type of work your machine will be doing. Because not all greases are the same, different greases should be used for different needs. Using the wrong grease for a specific application could lead to downtime and setbacks.
2. Understand the importance of grease thickeners and compatibility
Grease has similar base oils to diesel engine oils and tractor hydraulic fluids, but the ingredient that sets grease apart is the thickener. Metallic soap thickeners, such as lithium, lithium complex or polyurea, are the most common thickeners used in grease and work to hold the product’s base oils and additives together. For situations involving high temperature or increased load carrying capacity, a grease with a complex thickener is often recommended because it has better stability in these situations.
In addition to knowing which type of thickener is best for your needs, it’s just as important to know that the greases you’re using are compatible with each other. In fact, if two incompatible greases interact, it can cause a chemical reaction that stops them from lubricating, leading to harmful wear that puts your equipment at risk.
To make selecting compatible greases easier, the Cenex® brand created a line of premium grease products designed with simplicity in mind. Five of the Cenex greases found on farms today are compatible with each other because of their lithium complex makeup. Choosing Cenex products with a lithium complex is a safe bet for compatibility, but always refer to the grease compatibility chart first when making greasing decisions. This chart is a just guide, so if you have any questions, reach out to your local Cenex dealer.
3. Identify a high-quality grease
There are many different types of grease on the market, and you can identify a high-quality product by checking the cartridge, label or grease keg. Companies that supply high-quality products provide additional information for the consumer to review to help them understand the quality. Using a high-quality grease not only helps extend the life of your equipment, but it also prevents contamination and improves machine performance. Here are a few factors to look for in a high-quality grease:
a. Consistency
The National Lubricating Grease Institute’s (NLGI) ratings uses a numerical scale ranging from 000 to 6, classifying the consistency of greases. The lower the number, the more fluid the grease; the higher the number, the thicker the grease. When selecting a grease on the NLGI scale, most people use a #1 or a #2, which are both all-purpose greases. A #1 grease is lower on the NLGI scale, so it has less thickener, which allows it to flow easier than a #2 grease, making it a better choice for colder months to keep key components protected. Because #2 greases have more thickener, they’re stiffer and are better suited for use in warmer months when temperatures reach extreme highs. The NLGI rating indicates a high-quality product since low-quality products wouldn’t display this information on the cartridge or label.
b. Synthetics
Synthetic greases, like Maxtron® FS full-synthetic lithium complex grease, are built to handle temperature fluctuations. This means using a synthetic grease sets you up for success no matter the conditions because they allow for optimal lubrication to handle heavy loads or severe conditions.
c. Complexing
A lithium complex grease possesses many of the same properties as a simple lithium soap grease, but it has different sized strands and densities that allow for better performance in extreme conditions. Think of a sponge. A simple lithium grease is like a sponge with large holes. It holds the base oil in place, seeps out to protect equipment and then is reabsorbed into the sponge once operating is complete. A complex grease, on the other hand, is like a sponge with small holes. It holds more of the base oil longer, creating a more stable product.
Selecting the right grease is a critical decision in keeping equipment operating smoothly. The full line of Cenex premium greases is carefully formulated to extend equipment life and reduce maintenance costs by delivering outstanding protection in the toughest conditions.
To help determine which grease suits your equipment needs, see the equipment lookup tool and contact your local Cenex dealer.